Haoming Rong & Ramaiah Kotra
INTRODUCTION
The production of nonwoven fabrics is carried out as either a
continuous process, with fiber or resin as the input material and a roll
of fabric as output, or as a series of batch processes. Correspondingly,
fabric finishing is carried out either in tandem with web formation and
consolidation or off-line as a separate operation. Nonwoven bonded fabrics
are, by definition, textiles and they can be finished in exactly the same
way as other textiles such as woven or knitted fabrics. There are many
examples of particular methods and types of finishing equipment being used
for both kinds of fabrics. Nonwovens may be given one or more of a variety
of finishing processes as a means of enhancing fabric performance or
aesthetic properties. Performance properties include functional
characteristics such as moisture regain and transport, absorbency, or
repellency; flame retardancy; electrical response; resistance; and
frictional behavior. Aesthetic properties include various attributes such
as appearance, surface texture, color, and odor.
Finishing of nonwoven bonded fabrics can be classified
from different ways. Some people believe nonwoven finishing processes can
be categorized as being either chemical, mechanical, or
thermal-mechanical. Chemical finishing involves the application of
chemical agents as coatings to fabric surfaces or the impregnation of
fabrics with chemical additives or fillers. Mechanical finishing involves
altering the texture of fabric surfaces by physically reorienting or
shaping Fibers on or near the fabric surface. Thermal-mechanical finishing
involves altering fabric dimensions or physical properties through the use
of heat and pressure [12]. Generally, finishing of nonwoven bonded fabrics
are classified as (I) Dry finishing and (II) Wet finishing.
DRY FINISHING
Shrinkage
The compression which accompanies shrinkage is useful
in obtaining greater basis weight or GSM (grams per square meter) and
density, more bulk, higher strength and improved cleavage properties.
Shrinkage occurs when the Fibers are wet or dry depending on the type.
Shrinkage by exposure to heat is suitable for a nonwoven fabric made
predominantly of synthetic Fibers and is especially effective if Fibers
are prone to shrinkage. The web is fed through the heating zone on screen
driers. Thers are usually perforated cylinder driers with a rotating
overfeed, whereby the web is fed faster onto the roll than it is drawn
off.
A second shrinkage is carried out if the web contains
significant amounts of natural Fibers. The web is immersed in a tank of
hot water to promote shrinkage and is dried without tension. Some special
synthetic Fibers shrink both when they are wet and when heated. A
variation of wet shrinkage, which aids in saving energy, is shrinkage in
steam. Needling together two types of webs where one shrinks and the other
is shrink-proof results in the formation of decorative raised patterns
when shrunk. This technique is used in the production of sculptured wall
and floor coverings.
Wrenching
The Clupak process, invented by Sanford Cluett, is
similar to the sanforising process first used in the paper industry in
1957. It was later adopted to wet-laid nonwoven bonded fabrics.
Figure 1
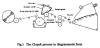
The machinery (Fig.1) consists of a continuous rubber
belt, about 25 mm thick, with an intermediate woven layer lying on a
heated, chromium-plated and polished drying cylinder. The web is pressed
against the cylinder at the first point of contact by a non-rotating
clamping bar. The rubber cloth is compacted lengthwise, which affects the
web between it and the cylinder in the same way thus causing compacting
and crimping of the Fibers in the web longitudinally. The web is fed
moist, through the gap between the belt and the cylinder. The compacting
is fixed by drying.
The outcome of the Clupak method depends on a number of
factors. Hydrophilic Fibers are more suitable than hydrophobic ones.
Polyolefin Fibers are not suitable due to their lower moisture absorption
and sensitivity to heat. Webs in which the Fibers are oriented lengthwise
give a more pronounced effect than cross-laid or random-laid webs. The
degree of wrenching is increased if the moisture content is high - about
20% - but if the bonding agent is high (> 50%) such increases are
unattainable. Thermoplastic bonding agents assist wrenching but the web
tends to adhere to the cylinder. Elastomer bonding agents due to their
elastic nature almost cancel the wrenching effect.
Creeping: The Micrex-microcrepe process
In the Micrex process, compaction of the web is so
strong that the creeping effect is visible and the increase in extension
and basis weight can easily be measured. The surface per unit area is
larger and the flexibility is improved even further than by the Clupak
method.
The apparatus for the Micrex processs (Fig.2) consists
of a rotating conveyor roller, the surface of which has screw- shaped
grooves in it, and two guide plates - one fixed and one elastic -forming a
knee lying against the cylinder. Between these is fed the web and nearby
is a scrapper-like compressing device inclined at an acute angle to the
surface of the roller.
Figure 2
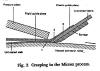
The web is compacted in the first gap, then raises
itself from the cylinder in the relaxation zone to be compacted by the
scrapper again. The process can be adjusted to produce a fine or coarse
crepe without significant impairment of the mechanical properties despite
production speeds of 150-200 m/min since the web is handled dry and at
much lower temperatures as compared to the Clupak method. This method is
suitable to creeping longitudinally oriented carded webs, wet or dry-laid
random structured webs, spun-bonded and spunlaced products.
Crabbing,Calendering and Pressing
These methods are used to improve the surface
characteristics of the fabrics, the most important features being
smoothing and patterning. The processes used are continuous and usually
involve one or several pairs of rollers operating under pressure.
- Glazing or Rolling calender: This method is not particularly
important for nonwoven fabrics, with occasional exceptions. The smooth
surface can be obtained usually by selecting an appropriate form of
bonding and, especially, for drying a wet-bonded web. Calendering has
not met with much success since it is often accompanied by undesirable
compression. The only time a rolling calender is used is when two steel
rollers are paired to break the so-called 'blotches' in spun-bonded
fabrics.
- Moire or goffering calender: The calenders are common in nonwoven
finishing and are used in the compacting of the webs made of natural and
synthetic Fibers. This type of calendering can be considered to be both
a bonding and finishing process. Webs composed of longitudinally
oriented cotton or viscose Fibers with a GSM of about 10-30 g/m2
can be stiffened and compacted sufficiently by passing them through a
goffering calender when slightly damp. Hot embossing of synthetic fiber
webs, even when the Fibers are longitudinally oriented, produces a
product remarkably strong due to the Fibers melting at the embossed
areas. The patterns can be of grid, webbed or point type. The
temperature of the heated rollers is generally 20-30
C above the melting
point of the Fibers and the nip roll pressure 20-50dN/cm, depending on
the volume of the web and the proportion of synthetic Fibers it
contains. If the web is cross-laid, point embossing results in maximum
strength. If the Fibers are arranged lengthwise, webbed embossing is
employed.
The embossing effect is used to obtain special
effects such as leather graining, simulated weave, plaster, brush
strokes, cord and mock tiling. Another area in which heated calenders
are used is in the manufacture of laminates. Here thermoplastic
Fibers, layers of thread or film are placed between two layers of
non-plastic web and are fused together by heat and pressure. Such
laminates are used as tablecloths, seat and cushion covers. Calenders
are also used in the transfer printing of the bonded webs.
- Roller presses: The oldest form of improving the surface of nonwoven
bonded fabrics is the pressing of wool felts, especially felts for
collar linings. This gives a smoother surface finish and also improves
strength and luster.
Perforating and Slitting
The nonwoven bonded fabrics produced are too stiff and
are, therefore, unsuitable for clothing. This is because the individual
Fibers are not free to move in relation to one another, as are threads in
woven or knitted fabrics. Perforating and slitting are two methods
practiced to improve the fall or drape of nonwoven bonded fabrics.
- Perforating: The Artos method is a method of perforating in which
the web, which has been bonded by using chemicals, is perforated with
hot needles. This process not only punches holes but also reinforces as
a result of cross-linking and condensation of the bonding agent. The
Hungarian firm Temaforg uses a similar method to perforate webs
made of synthetic Fibers to produce nonwoven bonded fabrics which are
strong and yet supple enough for use as building and insulation
materials.
- Slitting: Slitting, originally developed to improve the softness and
drape of films was used by the Breveteam company for interlinings, in
particular for adhesive fixable interlinings. The optimum cut length and
distance between the slits to get maximum softness and fall without
serious reduction of strength can be calculated. The effect of slitting
allows greatest flexibility at right angles to the direction of the
slit.
The slitting is accomplished by a roller with small
blades mounted on it, for example, in an off-set arrangement 1.7 mm
apart, making slits of a maximum length of 6.5mm. Rotary knives with
spreaders can be fitted to the roller, thus making an interrupted
cutting edge. Polyethylene or polyamide film shaped by splitting or
embossing and stretching by the Xironet and Smith-Nephew methods make
good air permeable bonding layers for laminating nonwoven bonded
fabrics.
Splitting, Grinding, Velouring and Singeing:
- Splitting: When nonwovens are substituted for leather, the thick
layer of needled fabric is split similar to the splitting of leather to
make thinner fabrics. The fabrics used are thick, high strength, firmly
bonded, closely needled and usually shrunk. The product is thin, supple
and like leather is used for slip belts, shoe interlinings, backing
material for shoe uppers and leather bags.
Splitting is done by machines in which a continuous
rotation hoop knife is guided with great precision in the gap between
two conveyor rollers, the distance between them depending on the
thickness and type of fabric required.
- Grinding and Velouring: Splitting is followed by either ironing and
friction calendering or moire calendering and possibly also grinding and
polishing to make the surface even, giving the fabric the appearance of
velour or suede. The process is known as velouring. First there are
several machines or consecutive passages to coarsely roughen the surface
and then polish it increasingly fine. After grinding, the dust is
removed by brushing or beating the fabric or by suction. The distinctive
features of such products are their soft feel, elegant draping qualities
and velvet-like surface.
- Singeing: Singeing also belongs to the category of a dry finishing
process. It is essentially the burning off of protruding Fibers from
nonwoven fabrics, particularly needled fabrics. The process is exactly
the same as traditional singeing and is carried out on gassing frames
where the fabric is passed over an open gas flame. The surface is made
smoother, which simplifies the dusting of filter fabrics.
WET FINISHING
Washing
The purpose of washing is to remove unwanted substances
from the fabric. In a wet process a suitable washing machine, using water
as the washing medium and occasionally a detergent, intensifies the
effects required.
Some anionic washing agents also have the effect of
softening the fabric; nonionic agents have the advantage of being
universally compatible but are more efficient at specific temperatures. As
in all wet and dry processes the fabric should be subjected to as little
tension as possible when being washed and, lengthwise, stretching is
undesirable.
Dyeing
Nonwoven fabrics are colored either plain or patterned
when they are to be used for decorative purposes. Examples are in
wallpapers or floor coverings, table or bed linen or as a furnishing
fabric. The interlinings for shirts or blouses are also colored to match
the top fabric. Colors can be divided into dyes and pigments. Dyes have
substantivity for Fibers, meaning they are attracted from their
application media by the fibrous substrate. Pigments are applied from a
latex medium. Both dyes and pigments can be applied at various stages of
the nonwoven process, starting from the polymer or pulp of Fibers prior to
web formation.[6]
- Dyeing of polymer: In certain polymers like polyester dyes and
pigments can be added as a concentrate to the polymer immediately prior
to extrusion. This process is referred to as producer coloration or melt
dyeing. The color concentrates are usually pellets or beads that contain
a high concentration of dyes or pigments. Acrylic polymer can be "gel
dyed" with cationic dyes which react with the anionic sites in the
polymer while the polymer is in the final stages of being formed prior
to drying. In rayon, pigments can be introduced to the polymer solution
prior to spinning. This is also the case in polypropylene, which has
much less affinity to dyes. The advantages of producer coloring is that
the web does not have to withstand the rigors of dyeing and the dye
fastness is generally superior to dyed webs.[7]
- Staple and mass dyeing: Dyeing and printing are wet processes and
are time, energy and cost-intensive. Wherever possible, coloring of the
web is combined with the wet processes necessary for the bonding, or the
fiber is dyed in staple form. Mass dyeing plays an important role in the
case of synthetic Fibers.
- Dyeing and bonding: When the web has to be bonded chemically the dye
is also added to the vat containing the bonding agent. The bonding agent
may coat the Fibers of the web equally, which would make possible the
use of finely dispersed pigment dyes. The bonding agent would then
adhere to the surface of the Fibers and also would exhibit the excellent
non-fading properties pigments are noted for. This also improves the
rubbing fastness when wet or dry and dye fastness to perspiration and
ironing. In the case of bonding agents not applied evenly to all Fibers,
a dye with affinity to the Fibers can be added to the medium containing
the bonding agent. Thus even dyeing can be expected despite the uneven
distribution of the bonding agent.
If great lengths of web composed of a single type
of fiber, bonding and dyeing can be carried out in a single process
without difficulty. For example cotton and viscose webs can be dyed
with direct dyes, polyamide webs with acidic dyes and polyester webs
with disperse dyes resulting in coloration that is as deep and fast as
conventional dyeing. The only consideration is that the pH of the
bonding agent be acceptable for the dye.
- Subsequent dyeing: It is much more difficult to dye and bond
simultaneously if the web is composed of a mixture of different kinds of
Fibers. In this case and also in many cases when the fiber is
homogeneous, dyeing is carried out in a later stage. The nonwoven fabric
is then treated as a woven of knitted fabric and is dyed in the
traditional ways.
Heavy and high bulk fabrics are dyed continuously
since jiggers or dyeing beams, which work in batches, can cope with
only small quantities and is therefore not economically feasible. It
is however possible to dye light nonwoven fabrics perfectly on dyeing
beams. Thermoplasticity, especially of the soft acrylate bonding
agents, play an important role in jig dyeing. Polyester nonwovens can
be jig dyed at a high temperature, but it has been found that at
temperatures above 102 C the bonding agent begins to make the separate
layers of the web adhere to one another. Consequently the rolls do not
unwind properly.
- Cold pad batch dyeing: This process was patented by Farbwerke
Hoechst for the dyeing of bonded webs made from polyamide by the cold
pad-batch method. Nonwoven fabrics meant for curtains and table linen
produced by the melt spinning or card/cross-laying method and bonded
with acrylic acid esters are dyed with acid or metal coupled dyes to
which acids are added to provide hydrogen bonding together with cold
wetting agents to encourage migration. The fabric is then padded,
batched and left for 24 hours covered with polyethylene film to be
roller burnished. Later it is given a warm rinse followed by soaping
and, thereafter, a further rinse.
- Continuous dyeing: The dyeing of heavy nonwoven fabrics is
continuous, usually by the conventional pad-steam process followed by
steaming to fix the dye. Steaming is usually followed by rinsing and
washing.
Printing
Due to the increasingly popular use of nonwovens in the
home furnishing sector there has been a great expansion of the color range
and printing methods. The most commonly employed methods are screen and
rotary screen-printing. The nowoven fabric is placed on the printing
backcloth similar to any other fabric and printed with dyestuffs
appropriate for the fabric concerned, partially dried, fixed by steaming
and washed.
Pigment printing is very important since the pigment
binders bond the fabric even more. The effect is particularly marked in
spunbonded fabrics. A further consequence is that condensation replaces
drying and steaming. If the thickeners have little body, washing may not
be necessary.
- Printing of light non-woven bonded fabrics: Pigments are suitable
for all kinds of light, non-woven bonded fabrics. The concentration of
dye is high in light fabric printing.
- Printing heavy non-woven bonded fabrics: The printing paste for the
rotary screen printing of heavy needled fabrics have very different
rheological properties from the paste suitable for light fabrics. The
printing speed is much lower than when printing light fabrics.
- Transfer printing: In transfer printing, subliming dyestuffs are
transferred from a release paper on to the non-woven bonded fabric with
the aid of heat and pressure. Polyester fiber is more suitable for this
method.
Chemical finishes
Nonwovens are finished with various chemicals in order
to obtain the specific property depending on end-use. Different chemical
finishes are discussed below.
- Antistats: Static electricity tends to build up in nonwovens made of
synthetic Fibers due to their lack of moisture regain and conductivity.
This can cause problems such as clinging and dragging during processing,
apparel that clings and crackles, dangerous discharge of static
electricity in explosive atmospheres and tendency to attract airborne
dirt and soil in processing and use. The antistats work in three basic
ways. They improve the conductivity of the Fibers, coat the fiber with a
thin layer of material that will attract a thin layer of moisture, and
finish the fabric such that it holds a charge opposite to that normally
accumulated on the fiber to neutralize the static charge. Antistats can
be either durable or non-durable. Examples of durable antistats include
vapor deposited metals, conductive carbon or metallic particles applied
by binders, polyamines, polyethoxylated amine and ammonium salts and
carboxylic salts. Non-durable antistats usually consist of inorganic or
organic salts or hygroscopic organic materials. Examples are quaternary
ammonium salts, imidazoles and fatty amides which are cationic. Anionic
antistats include phosphates, phosphate esters, sulfonates, sulfates and
phosphonates. Examples of nonionic antistats include glycols,
ethoxylated fatty acids, ethoxylated fatty alcohols and sorbitan fatty
acid esters.
- Antimicrobials: These are used to control populations of bacteria,
fungi, algae and viruses on the substrate. The treatment usually
prevents the biological degradation of the product or prevents the
growth of undesirable organisms. Broadly classed, the antimicrobials are
either fixed or leachable. The fixed treatments are durable, but the
leachable treatments may transfer to the surrounding environment through
migration, solubility or abrasion. A generic list of the treatments
include alcohols such as isopropanol or propylene glycol, halogens such
as chlorine, hypochlorite, iodine, N-chloramine and hexachlorophene,
metals such as silver nitrate, mercuric chloride and tin chloride,
various peroxides, phenols quaternary ammonium compounds, pine oil
derivatives, aldehydes and phosphoric acid esters. Care should be taken
in the application of these compounds to prevent inactivation, loss of
durability or masking of the active ingredient with other finishes.
- Water repellents: Water repellent finishes are a type of barrier,
which function to lower the critical surface tension of the fiber
surface. To be most effective it is important that the Fibers are
treated evenly on all surfaces to give the lowest critical surface
tension possible. Water repellency can be achieved with a variety of
chemical finishes such as waxes, wax dispersions, melamine wax
extenders, chrome complexes, silicones, and flourochemicals. The
finishes require curing to develop the best repellency and are also
prone to destabilizing with shear, heat or changes of pH or ionic
strength.
- Lubricants: Lubricants or slip agents are generally applied as
processing aids to help in stretching or to improve the processability
of nonwovens. They are also applied to aid in sewing, quilting, tufting
or other processes where needles penetrate the fabric. Lubricants impart
the same properties as softeners but specifically reduce fiber friction.
Common chemicals include sulphonated oils, oil emulsions, silicones,
esters, polyethylene dispersions and fatty acid soaps. Many surfactants
may also be used. Care should be taken to avoid excessive strength loss.
- UV absorbers and polymer stabilizers: Ultraviolet light can do great
damage to the polymers causing photo-degradation, yellowing, loss in
strength and fading of the colors. The damage is generally due to the
formation of destructive free radicals in the polymer. The finish can
protect the fabric by shielding the fiber or absorbing the light or by
chemically quenching the free radicals. The three main classes of
products used are, substituted benzotriazoles, benzophenones which are
uv absorbers, and hindered amines which are free radical reactants. They
are applied from a bath or added to the polymer.
- Flame retardants: The finishing of fabrics with flame retardants can
reduce the tendency to burn or reduce the tendency to propagate the
flame. The flame retardants may char the fuel, quench the reaction of
combustion, absorb heat or emit cooling gases or replace oxygen. Flame
retardants are durable or nondurable. Durable retardants include
decabromodiphenyl oxide, antimony oxide, phosphates, brominated esters,
PVC and other chlorinated binders. Nondurables include borates, boric
acids, zinc borate, sulfamic acid sulfamates, ammonium phosphates, urea,
etc. Hydrated alumina and zinc borate act as smoke supressants. Problems
in the application include odor, yellowing, loss of tensile strength,
stiffening, skin irritation and color change or loss.
- Softeners: Softeners are applied to improve the aesthetic and
functional characteristics of a fabric. The hand, drape, abrasion
resistance, sewability and tear strength can be improved with the
addition of a softener. It works by reducing the coefficient of friction
between the Fibers. There are different types of softeners such as
anionic (sulfates or sulfonates), cationic (amines and quaternary
amines) and nonionic (silicones, ethylene oxide derivatives and
hydrocarbon waxes.)
- Absorbency and rewetters: Chemicals used to impart hydrophilicity to
a nonwoven are referred to as rewetters. These treatments increase the
critical surface tension of the fiber making it more wettable. This
property is desirable in end-uses such as wipes, hygiene, medical
absorbent pads and garments. For hydrophobic Fibers the treatment
facilitates the movement and penetration of the liquid in the capillary
channels. Many anionic and nonionic surfactants, antistats, flame
retardants and softeners impart hydrophilicity.
- Thermoplastic binders, resins and emulsion polymers: Binders and
resins are widely used in the finishing of nonwovens to add strength,
control stiffness, add moldability or pleatability, provide durable
flame retardants, color, reduce linting and control shrinkage. They
soften when exposed to heat and return to their original state when
cooled and, hence, can be set. Emulsion polymers are also called
latexes. The common binders, resins and polymers include acrylics, PVC,
polyacrylic acid, urethanes, starch, vinyl acetate etc.
- Thermosetting resins and crosslinking agents: These are used to
produce wrinkle resistant or permanent-press textiles. They are used to
crosslink cellulose for wrinkle resistance, crosslink binders for wash
durability and solvent resistance. The technology is based on the
ability of formaldehyde to react with cellulose and nitrogen containing
resins. The important resin types are melamine-formaldehyde, urea
formaldehyde and dimethyloethylene urea. The reaction is usually
catalyzed by acids, such as Lowry-Bronsted or Lewis acids. Problems
encountered include formaldehyde generation, tensile loss, discoloration
and amine odor.
- Soil release: The soil release chemicals reduce the problem of
soiling in two ways: repel the stains and soil using repellants such as
flourochemicals or create a surface that aids the removal of soils when
cleaning or laundering using chemicals based on polyacrylic acid.
- Optical brighteners: Optical brightners or fluorescent whitening
agents are organic chemicals that are used like dyes or pigments to add
brightness to fabrics. These chemicals are colorless but can absorb UV
light and reemit it to the visible range usually as a blue or
blue-green. These products produce very white fabrics or brighten
colored fabrics.[8]
Coating
Coating is a basic and exceptionally important form of
finishing for non-woven bonded fabrics. The way in which the coating is
carried out depends on the substrate, the machinery available, the
substance that is to be applied and, also on the effect desired.
- Slop padding: It is one of the best known methods of direct coating.
The coating is put on with a rotary roller, the surface of which is
covered in the substance to be applied. The slop padding roller is fed
directly with the laminating float by being dipped into it or using
special feed rollers.
- Powder point method
- Coating by rotary screen printing
- Spreading or squeeze
- Non-contact coating
- Release coating
Laminating
Laminating is the permanent jointing of two or more
prefabricated fabrics. Unless one or other of the fabrics develops
adhesive properties in certain conditions, an additional medium is
necessary to secure bonding.
- Wet laminating: Adhesives used in the wet process are dissolved or
dispersed in a suitable solvent. The simplest form of wet laminating
consists of applying the adhesive to one of the lengths of material that
is to be joined, and to put the second length on it with the required
amount of pressure. Then drying, hardening or condensing the material
that has been joined together is carried out. The solvents can be
macromolecular natural or synthetic substances and water.
- Dry laminating: All Kinds of thermoplastics are used for dry
laminating. These include powders, plastisols, or melt adhesives, and
are applied to the substrates that are to be joined together using
suitable machinery. Dry laminated non-woven fabrics have a soft feel.
Flocking
Flocking is a process of making a two-dimensional
fabric have a third dimension. It is done by mechanically or commonly
electrostatically. Depending on how the adhesive is applied, the whole
surface can be flocked or patterns can be made. The adhesives are just
like what are used in laminating and include polyvinylchloride plastisols,
polyurethane bicomponent adhesives and all kinds of aqueous dispersion
adhesives.
New finishing development:
- A metallic meltblown nonwoven has been produced by Kimberly-Clark
under the brand name Demique. This has a basis weight of 1.5
ounces per square yard and offers a stretch of from 10-500%. Vacuum
metallized coatings may be from a few nanometers to several microns
thick[9].
- A kind of nonwoven fabrics used to provide high frequency
electromagnetic shielding has been developed. The fabrics were treated
with copper sulphides[10].
- A new type of battery separator has been invented that is made of a
blend-stretch type of nonwoven material based on hydrophobic Fibers
[11].
Research of Textile Finishing: SOLID-ON-SOLID
Many textile manufacturing operations such as dyeing, printing, and
finishing of fabrics use wet processing techniques. These techniques
involve using an aqueous solution or bath to apply chemicals to a textile
substrate, fixing the chemicals to the fiber, scouring or washing to
remove loose chemicals, and drying to produce a finished product. Heating
and later evaporating water make these wet processes very energy
intensive. Industry experts estimate that wet processes use approximately
60% of the energy consumed in the textile industry. In addition, shrinking
water supplies in many parts of the world have prompted textile
manufacturers to develop methods that reduce water and energy consumption.
Working in this direction Georgia Tech's School of Textile and fiber
Engineering has investigated three SOS technologies. One of the techniques
used electostatic powder spraygun deposition in the finishing of 100%
polypropylene nonwoven fabric. In this work, fluoropolymer in a fine
powder was used in making fabric having an excellent barrier to
oil/solvent and isoproponal. The trials demonstrated for the first time
that a finishing process, which combines powder deposition and melt
cutting can impart superior barrier properties to polypropylene nonwoven
substrate. So with the further developments in SOS processing, There can
result the elimination of the need for steam generation, the elimination
of effluents, a decrease in dwell times in the curing oven, the reduction
of water consumption and the saving of energy. These changes can increase
productivity and reduce costs[13].
- Menachim Lewin and Stephen B. Sello, Chemical Processing of Fibers
and fabrics, Functional Finishes, Part B, 1983.
- G H J Van der Walt and N J J Van Rensberg, Low-liquor Dyeing and
Finishing, Textile Progress, Vol. 14, No. 12, 1984.
- Howard L. Needles, Textile Fibers, Dyes, finishes and Process, A
Concise Guide, University of California, Davis, CA, 1986.
- J. Robert Wagner, TAPPI Journal, Vol. 66, No. 4, pp 41-43,1983
- Herman b. Goldstein and Herbert w. Smith, aatcc, Vol. 12, No. 3, pp
49-54, 1980.
- J. R. Aspland and C. W. Jarvis, Clemson University, Clemson, SC, The
Coloration and Finishing of Nonwoven fabrics
- J. K. Vandermaas, Hoechst Celenese Corp and J. R. Aspland, Clemson
University, Dyeing of Nonwovens.
- Frank Baldwin, Precision fabrics Group Inc, Greensboro, NC, The
Chemical Finishing of Nonwovens.
- Metallization of elastomeric fabrics, High Performance Textile,
January 1998.
- Producing conductive Fibers, High Performance Textile, July 1997.
- Finishing-Hydrophilic transformation key to battery separator, High
Performance Textile, March 1996.
- http://www.nonwovens.com
- http://es.epa.gov/techinfo/facts/solid-cs.html
Apparel Search
Add Your Company Contact
Us About Us Advertise
News Letter Legal
Help
Copyright © 1999-2023 Apparel Search Company. All Rights Reserved.
Buy Fashion
For The Holidays. |